The advent of 0.1% Sulphur Emission Control Areas (ECAs) from 2015 and the ensuing switch to costlier distillate fuels with lower sulphur content will only add to fuel cost concerns for owners and operators. The cost challenges posed by ECA’s will increase in Europe by 2020 when the EU will introduce a Europe-wide ECA and globally, through the IMO, by either 2020 or 2025.
Moreover, demonstrating these marked savings comes with further requirements too. The IMO’s ship energy efficiency management plan (SEEMP) entered into force in January 2013, mandating that shipowners and operators provide a clear performance benchmark of their vessels to provide transparency around vessel savings, while the Energy Efficiency Design Index (EEDI) is mandatory for new vessels.
But shipowners and operators are not the only parties to fall prey to the impact of legislation and rising costs – charter rates for many oil tankers and bulk carriers, currently do not cover vessel operating costs. Many charterers pay for fuel and so are often transporting their cargoes with little, or no profitability locked in.
In an industry where bunker fuel costs can account for as much as 80% of vessels’ expenditure and with charterers under such strain, it is little wonder that ‘demand side pull’ is increasing in the market; where charterers are increasingly influencing owners’ and operators’ operations.
As a result, demand for credible, proven technologies and measures to combat these challenges is unsurprisingly growing increasingly insatiable. While any fuel saving is a benefit, investment in fuel saving technology with a competitive payback period is the preferred option.
Oceanfoil’s aerofoil sail, or ‘wingsail’, is a propulsion assist technology particularly suited for tankers, as the vessel shape gives ample opportunity for the sails to catch the wind and convert it to forward thrust – thus reducing reliance upon the vessel’s main engines.
The results of model tests on a scaled 150,000 dwt Capesize bulker have shown that fuel savings of 15-20% can be achieved, depending upon weather conditions. Initially developed for the retrofit market, this technology has the potential to play a vital role in stemming high bunker fuel costs and meeting regulatory mandates.
Originally trialled in the 1980s on board the 6,000 dwt mini-bulker Ashington and showing a 15% saving during the trial period, the ‘wingsail’ was designed to play a fuel-assist role to a conventionally powered vessel. It enabled the ship to operate at the required speed with reduced engine propulsion.
Despite being hailed as a feat of innovative engineering 30 years ago, considerably lower bunker fuel costs at that time dictated that there was little need for a technology with a payback period far beyond current estimates of as little as two years.
Automatic control
Automatically controlled from the bridge, each ‘wingsail’ consists of three aircraft type wings mounted vertically with a single tail fin or rudder. Aircraft type slats on the trailing edge of each wing are computer controlled to ensure that the ‘wingsail’ is automatically angled to optimise the thrust generated for any given wind direction. This enables effective directional force for propulsion harnessed from the wind.
The number of ‘wingsails’ fitted depends on the vessel size and type, all of which is calculated before installation of the technology. The rudder reacts to more subtle wind changes, ensuring optimum propulsion positioning.
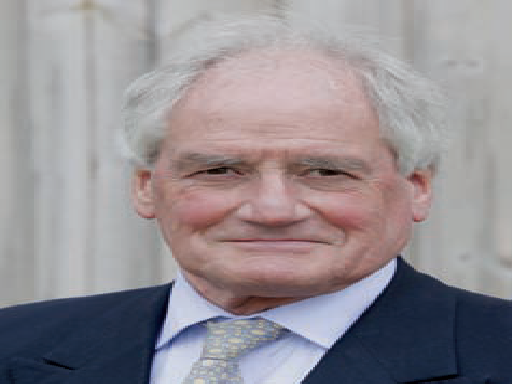
Oceanfoil’s Charles Moray.
The number of ‘wingsails’ fitted can be calculated to give optimum propulsion assist and fuel saving, smaller vessels may perform optimally under two or three ‘wingsails’, larger vessels could experience better savings with up to six ‘wingsails’. However, this can be adapted to meet the needs of the customer, fewer ‘wingsails’ would mean lower savings potential but may meet the customer’s needs, or serve as proof of concept for other vessels in the fleet.
Each ‘wingsail’ is mounted on a single bearing, which itself forms part of a mounting bracket fitted to the deck of the vessel. The design of Oceanfoil ‘wingsails’ and the method of mounting them on vessels ensure that there is no interference with cargo handling equipment and hatches/manifolds, on product, or crude tankers and many cargo ships. No crew training is required for its operation, as it is computer controlled from the bridge of the vessel.
What is clear is that the current global fleet has a huge potential to increase efficiency and profitability using proven technology that can be retrofitted. Oceanfoil’s technology comes with competitive payback periods and demonstrating this is the next step to supporting the industry in embracing this solution.
Investment in innovative double digit saving technology, such as that proposed by Oceanfoil, can help support a new era within in the industry where wind power can by utilised to support the shipping industry, as it looks to marry growth with sustainability.
*This article was written by Charles Moray, managing director, Oceanfoil Limited.